A warehouse management system (WMS) is a software solution and a process that allows organizations better visibility of their inventory and enables smooth administration of warehouse operations from the time goods or materials enter a warehouse until they move out.
Introduction
In this article, we will cover:
- What is a warehouse management system and how does it work?
- What types of warehouse management systems and warehouse management software can you buy?
- Barcode scanner, Batch (Lot), Expiration date handling
- What are the benefits of a WMS?
- An example of a warehouse layout
- The WMS process and best practices
- A comparison of standalone and integrated WMS
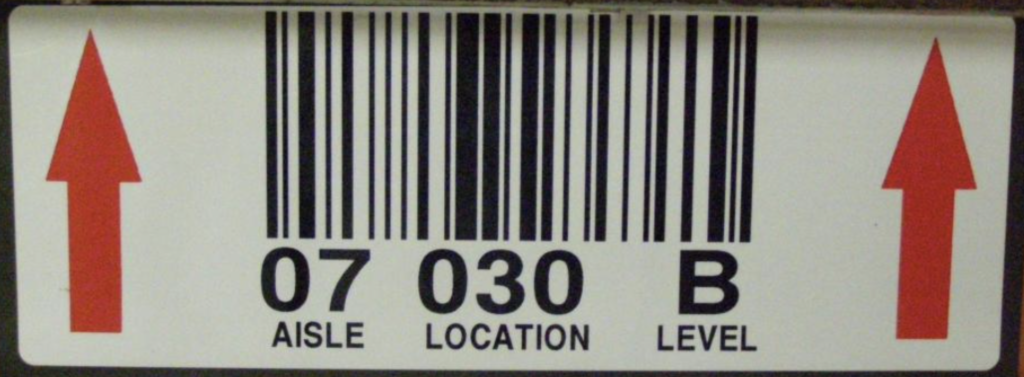
What is a warehouse management system and how does it work?
A warehouse management system (WMS) is a software solution that is widely used in manufacturing, retail, warehousing, and many other industries to track all materials and goods as they come in and go out of the warehouse. It provides visibility of the inventory and helps optimize all warehouse processes. A warehouse management system (WMS) is software that is designed and built to optimize the warehouse, distribution, supply chain, and fulfillment processes within a business.
It is very important to organize the materials and goods in a warehouse so that they can be found quickly when needed. For many products such as perishable items, health care products, and others, it is vital to know the batch (or lot) number and expiration date of products in the warehouse. A WMS allows tracking of the products as well as provides alerts to replenish goods and materials in time.
The system should not only track the materials in the warehouse, but it must also streamline how workers pick products and pack orders. When a customer places an order, it can immediately check if the products are available. Instead of a person manually cross-referencing the order and the stock, the warehouse management system can automatically mark the order as ready for fulfillment. This saves a great deal of time and effort.
Besides picking, packing, ship, the WMS also provides the ability to track merchandise entering the warehouse. All received items are cross-checked with the purchase order and put in the appropriate shelve and bin so that they can be easily picked up when needed.
With the barcode scanner, product label printing, purchase order, sales order, and inventory management which can support multiple warehouses – a warehouse management software which is configured for a specific warehouse location can save a great deal of time for warehouse workers, improve overall productivity, and provide you an immediate return of investment.
Some of the basic WMS functionalities include:
- Inventory management
- Tracking stock location, batch (lot), expiration date
- Automate warehouse processes using barcode and barcode scanning
- Order receiving functions
- Order shipping functions
- Warehouse capacity management
- Record keeping functions
Example of organizations that uses WMS software:
- Manufacturing
- Retail
- Healthcare
- eCommerce
- Distributor
- Government
Types of Warehouse Management Systems
Integrated Vs Standalone WMS
There are two types of warehouse management system software to handle warehouse operations that you can find: Integrated WMS and Standalone WMS.
An integrated WMS software is usually referred to as a solution that is part of your Enterprise Resource Planning (ERP) or other back-office solution. It may also come as an add-on module of an ERP system. Basically, in an integrated solution, the inventory, warehouse, order, invoicing, and other data are kept in the same database system. When everything is integrated into one system, it’s much easier to keep track of all the operations.
Pros:
Centralized data: All the inventory, warehouse, order, and invoicing data are kept in the same database. This allows you to have real-time access to data and consistency of the operation.
Simplified business scenarios: Integrated WMS is built on top of the ERP system and so the workflows are designed for end-to-end business scenarios such as order to cash. This will make it easier to execute the scenarios.
Better use experience: It provides a better user experience – since the product is running from the same database the user interaction flows are well connected, and a smaller number of clicks are needed to perform any tasks and can use the same login mechanism.
Cons:
Reduced functionality: Since this is not a specialized WMS software, most integrated WMS tend to have fewer functionalities.
A standalone warehouse management system software is feature-rich software that primarily serves the function of warehouse management. It may be integrated with order management or inventory management system, but the focus is purely on warehouse management. Therefore, it might have limited functionality for other aspects of your business. Since it is tailored to warehouse management, this type of WMS can have advanced reporting features that will help you level up your warehouse.
Pros:
Advanced Functionality: A standalone WMS often provides advanced picking functionalities with various options for picking suggestion algorithms as well as advanced reporting.
Integration capabilities: Standalone WMS software provides integration functionalities to integrate with 3rd party ERP systems.
Cons:
User workflow is complex: The workflow is often complex since the user must use two different systems, WMS, and ERP to complete the operation. It is time-consuming and error-prone.
Lack of real-time integration: Since data are in two different systems, ERP and WMS, the data are often not synchronized, and so real-time visibility is not available.
Increased cost: You need to buy two different systems and implement the integration. This will add to the cost of ownership of the WMS.
On-premises Vs Cloud-based WMS
Buying an on-premises WMS means you are responsible for setting up hardware (computer server), and network, and installing WMS software in it. This will give you complete control of the system as well as it may give you better latency. But it comes with a larger upfront cost since you need to set up the hardware landscape, and you will also need your WMS regularly maintained. Depending on the size of your operations, you may need to employ IT specialists to set up and regularly maintain your WMS system.
Alternatively, cloud-based WMS systems are hosted on a remote server. You will simply log in from your browser, barcode scanner, or mobile app and use the application. Things like bug fixes and software updates are handled by the vendor. The vendor will provide a guaranteed level of service uptime. You are charged on a subscription basis – mostly you will pay a yearly subscription with three years contract.
Many large businesses with a large number of distribution centers for eCommerce tend to maintain on-premises WMS. This is because the response time of the system (latency) is very important for them since they need to handle thousands of orders per day. Having complete control of the system will allow them to be more productive.
FAQ:
- What are Inventory Management Systems, Sales Order Management, and Purchase Order Management Systems?
Why use Warehouse Management System (WMS)?
There are many benefits WMS software can bring to your organization. You can process order faster, reduce the cost of operation of the warehouse as well as make more data-driven decisions to maximize your productivity and increase the return on investment (ROI).
Faster Order Fulfillment: In a fast-paced order fulfillment situation such as online order fulfillment, you need a warehouse management system to know what the stock level of each item is and in which warehouse location they are available, and which bin. This will reduce order processing time, cost, and errors.
Reduced Cost: A warehouse management system software can provide better visibility of what products leaving the warehouse. This will help you to optimize the arrangement of the warehouse so that you can store most often ordered items close to the loading area. This will shorten your order pickup time and reduce the cost.
Data-driven decision: Using WMS you can run your analytics faster which may help you in many ways. With the help of analytics, you can replenish products on a need basis. You can also predict the need for the stock for items in the short run and order those items in advance. This will help reduce your inventory cost and increase profitability. You can also find out the productivity of your warehouse workers and adjust the need for resources as your business needs.
Warehouse Management System for Small and Medium Sized Businesses
Small to Medium sized businesses thrive because they run their business optimally and efficiently. As they grow and the volume of orders increases, they face increased pressure to meet the needs of fulfilling orders in a shorter time. The businesses have not experienced these demands before and do not have the technology to help them meet the demands. Warehouses need to have the ability to change the traditional ways they have been doing business.
Implementing a Warehouse Management System (WMS) allows small and medium-sized businesses to rapidly increase current throughput and inventory utilization without increasing staff or floor space. It also provides the ability to meet the new demands and processes needed by their customers. This strengthens current relationships and helps bring on new customers for increased revenues.
Small to Medium sized businesses should be looking for a WMS system that also provides order management and inventory management systems. Having all these functionalities in one software will keep the cost down, manpower can just need to train in one application, and easily increase the operational improvements that produce a return on investment (ROI).
Warehouse Management System for Healthcare
Healthcare clinics and hospitals may not have large inventories and warehouses to store medicine and equipment, but they might have complex requirements for the supply chain. The pharmaceutical logistics can be challenging because many medications and medical equipment have specific storage needs, such as refrigeration, expiration date, etc. They are also bound by government regulations where recalls of medications and equipment are very strictly followed. A WMS can help healthcare facilities and distributors of medical suppliers to manage their operations efficiently.
Take a lot number (or batch number) functionality that is heavily used in the pharmaceutical industry. A WMS system can handle lot numbers and expiration dates. When goods are received, the lot number and expiration date for the received goods can be entered. The WMS will assign a bin where the received goods are stored. WMS can alert the closing expiration of the goods in the warehouse and their locations. WMS can also lead the picker to pick the close-to-expiry date goods at the time of customers’ orders fulfillment.
Evaluating Warehouse Management Software to buy?
Many factors determine which Warehouse Management System (WMS) software you want to buy. Some of the important factors you must consider are as follows:
- Your requirements: First thing to consider is your requirements. How many warehouse locations do you have? How many SKUs do you maintain? How many orders do you receive and fulfill per day? How many warehouse workers are working? Do you have any existing applications such as ERP? What are the pain points that you want to solve by using WMS? Having a clear requirement will help you to find out whether propose WMS is a fit for your requirements or not.
- Functionalities and extensibility of the software: Most of the WMS application covers inbound, outbound, return, transfer, and cycle count. Some of you need the flexibility of organizing workflows in the application. For example, can you do cycle counting by bin as well as a by-product? When looking for functionalities, you should look for flexibility to extend the existing application to your need.
- Cost: Cost is one of the important factors in choosing a WMS application. The cost of a WMS determines by the following factors:
- ERP: A Warehouse Management System needs an ERP to work with purchase orders, sales orders, invoices, bills, and inventory management. ERP’s inventory management system provides a holistic view of the inventory – i.e., you can view aggregated inventory from all the individual warehouse locations. WMS integrates with the ERP system by posting goods receipts or goods issues. Many WMS comes with integrated ERP. In such a scenario, you don’t have to purchase another ERP application. Standalone WMS application needs 3rd party ERP system to integrate. This may increase your cost.
- Implementation and Customization: Depending on the complexity of your WMS operation, you may need some customization in the WMS applications. If the customizations are part of the application configurations, then the cost is minimum. If customization needs coding, then you may need to pay more for this service. Also, if 3rd party applications such as ERP integration are required then the implementation of such integration may require a hefty fee.
- Hardware and Network: Some of the hardware and network fees are unavoidable. To use WMS, you will need a network – at least WIFI to run the applications on mobile devices. So, network and mobile device cost is a must. If you choose an on-premises WMS application, then you will need servers, file systems, as well a database. You must consider this infrastructure cost for on-premises WMS.
- WMS License or Subscription: For the WMS application you must pay a fee. If you are using on-premises WMS then you will be paying a one-time license fee and yearly support and maintenance fees. If you go for cloud-based WMS Software then you will be paying a yearly subscription. The yearly subscription will include support and maintenance fees and your WMS will be running on a remote server in the cloud which will be maintained by the vendor.
Best practice for managing your warehouse for barcode implementation
Warehouse management is a process you must design it thoroughly so that you can optimize your operations. Many times, you may think that sticking barcodes and scanning them is what you need – but this is just the starting. For example, to optimize the picking and put-away operations, you should consider the following:
- Grouping similar items and putting them close to each other in the warehouse
- Placing best-selling items near the packing area
- Barcodes should face outwards from shelves and upwards within bins
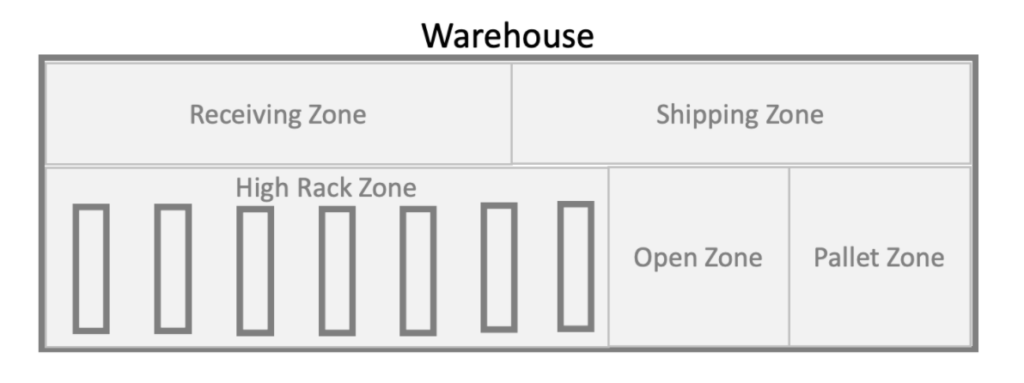
Warehouse Structure:
The first step of creating a Warehouse Management System (WMS) is to define the meaning the physical structure of your warehouse. Usually, you divide a warehouse into areas or zones where each zone is dedicated to a specific task. For example, you could have “receiving”, “packing”, “high rack shelves”, “open”, and “production material” zones in a warehouse. Separating warehouses in the zone will help you structure your overall warehouse area better.
A storage area or zone can be further divided into storage sections. For example, you have a “high rack” zone where you want to put fragile items in 1st two lower levels and regular items in the upper four levels. Here, you are effectively dividing the high rack into “regular” and “fragile” storage sections. A warehouse may not need this type of division of storage – but if it is required for you then you should create this structure so that when your workers put away items, the WMS can guide them accordingly. You keep your items in a storage bin in the warehouse. An overall structure of a warehouse can be visualized as:
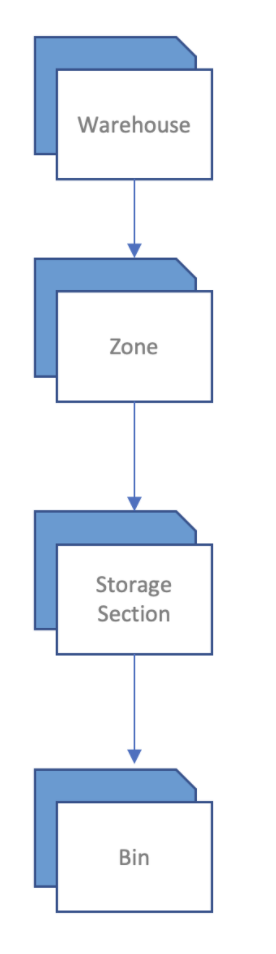
Warehouse configuration:
Warehouse: A unique name or number identifies a warehouse in WMS software. A warehouse number can represent a physical building, several physical buildings, or a section of the physical building. You create these locations in your Inventory Management System and assign a unique name to each warehouse. Then you use WMS to further configure a specific warehouse identified by a number or name.
For example, a manufacturing plant may have just one warehouse. It uses the warehouse for both raw materials as well as finished goods. But they may choose to logically divide this one physical warehouse into two in the WMS system. One for production material and another for finished goods and name them appropriately. It is also possible to keep one warehouse in the WMS but divide the area into zones: one for production and another for order.
Bin: A storage bin is the smallest physical unit or space available in the warehouse. So, it represents an exact position in the warehouse where items are stored. A bin is identified by a coordinate system. For example, a bin identified as 02-03-04 could be a storage bin in aisle 2, stack 3, and level 4. A bin can have a few attributes: maximum weight, total volume, and bin types (for example, items, pallets, etc.).
You can use any letter or number to create a coordinate system to uniquely name your bin. The purpose here is to enable warehouse workers easily to find the location of the bin. Here is an example of the bin coordinate system:
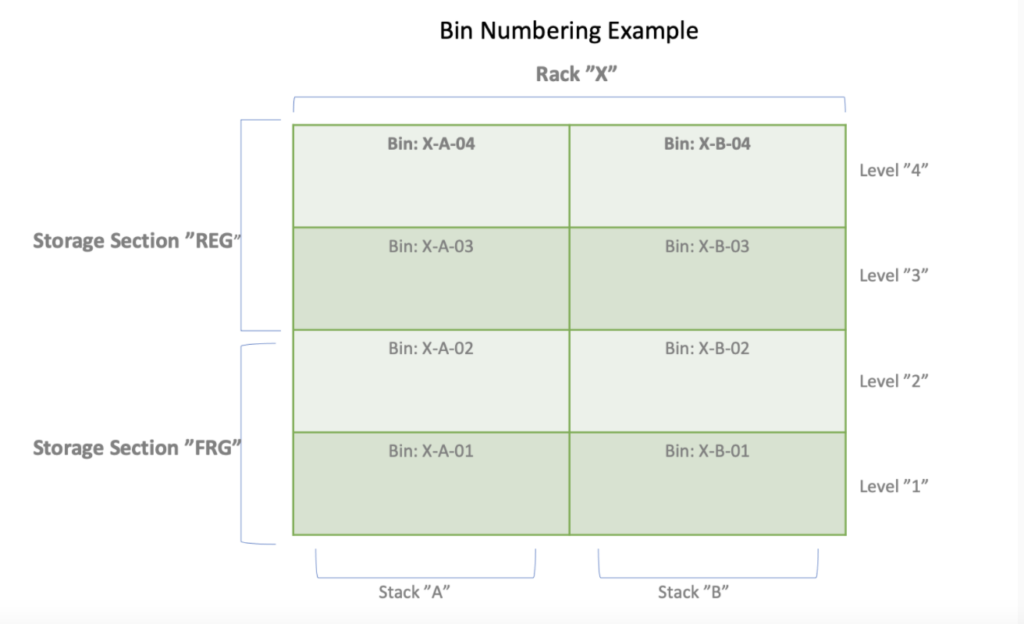
The Warehouse Management Process
A Warehouse Management System (WMS) has several functionalities. These functionalities are designed to complete specific workflow or scenarios. Some of these processes are described below:
- Picking: Workers pick products from the warehouse to fulfill customer orders. Warehouse picking refers to the process where individual items are picked to satisfy customers’ orders. In a large warehouse, picking items from the warehouse takes the longest time and so it is essential to design and operate the warehouse in such a way the picking time can be reduced.
- Goods Issue: A goods issue is about moving out of goods or materials from the warehouse. It means the issuing of goods or materials from the warehouse to the production, manufacturing process unit, or fulfillment of customers’ orders. When goods are issued, it reduces the number of available stocks in the warehouse. If the WMS system and Inventory Management System maintain different database tables for stock, then goods issue transactions will deduct the available stock of items in both the WMS and Inventory/ERP database tables.
- Packing: Packing is the process of putting items into bags or boxes to be sent to the customers. You can pack multiple orders in the same box or send each order in a separate package or add several orders packages in a pallet. You have complete control of how you want to pack and ship items to the customers.
- Shipping: After you pick and pack the order, the next step in the fulfillment process is to ship the order. Depending on the requirements, you may weigh the package, choose a carrier, print and stick a label on the package, and finally ship the order. These packages or pallets are then loaded in the truck for shipment.
- Receiving: The warehouse receiving process is one of the most important steps of supply chain management. An optimized receiving process can affect how you store, manage, and track your products. It involves unloading goods from delivery trucks, verifying the goods received against the purchase order, and issuing goods receipts.
- Goods Receipt: Goods receipt refers to the physical movement of goods into the warehouse from external vendors. When a goods receipt transaction is created, it always increases the stock of goods in your warehouse as well as in the central Inventory Management System or ERP. You can plan and manage your inbound deliveries and monitor the stock of ordered goods and materials.
- Putaway: The putaway process includes putting goods away in storage bins in the warehouse. In a warehouse, putaway refers to all the processes that happen between receiving goods from suppliers and having them all put away into their assigned locations. Having a putaway system simplifies the process of storing items, reduces the risk of misplacing or losing items, and keeps your warehouse clean and organized.
- Returns: Each business implements its return policy. Many warehouses use a three-bin system: return to inventory, discard, and return to supplier. Having a sorting system can be a huge time saver. You’re processing items in bulk rather than running each item to its destination. If you put back items into the warehouse, then your stock level of those items will increase. Discarding or returning to supplier goods will not change your stock level.
- Transfer: If you have more than one warehouse location and want to transfer goods from one location to another then you need to follow a goods transfer process. In this process, a goods transfer from one warehouse location to another is created. Using this request, you can pick items from the “sending” warehouse and when the transfer delivery is received in the “receiving” warehouse location, the same transfer request is used for receiving the goods. The Inventory Management System is used to create the transfer request.
- Cycle Counting: Cycle count provides the actual count of the items in the warehouse at a given moment – i.e. when the count is performed. WMS application provides a physical cycle count mechanism for warehouse workers to go around the warehouse and count the goods. Usually, two types of counting are performed: directed count where items and their current count are known, and blind cycle count where the item’s current stock level in the WMS is not shown to the worker. Physical inventory counts in the warehouse are labor-intensive, disruptive, and only accurate for that moment in time when the count occurs. The second that warehouse operations resume, the count is inaccurate and only has historical value. The WMS system usually provides the real-time count of all items.
Best Practice to Improve Efficiency in Warehouse
- Automate warehouse processes: To automate the order fulfillment process, let’s first understand the steps that usually need to take from the moment the customer places an order up to the shipment being loaded into the truck.
- Customer order goods from an eCommerce site.
- That order is downloaded from the eCommerce site to the order management system.
- The order is marked as booked depending on the available stock and other criteria such as payment.
- The order is sent to the WMS. The warehouse workers pick, pack, and ship the order.
In the above process, there is an opportunity to automate the (a) to (c) steps so that orders are automatically booked without any human interaction. This will hugely improve the efficiency of overall order fulfillment.
- Use barcode and barcode scanner: This WMS optimizes the supply chain process by eliminating errors, maximizing warehouse efficiency, and providing full end-to-end inventory traceability. It uses a mobile warehouse app on a scanner. To automate the process, make sure to label your bins and products so that you can use mobile devices to scan the barcode to confirm the pickup, putaway, or return of the products. This will hugely increase the efficiency of the warehouse operation.
- Use integrated Inventory management system: An integrated inventory management system is often referred to as the inventory management system which includes an order management system. And order management system provides sales order, invoice, quote, and purchase order management functionalities. A WMS which is built on top of an inventory and order management system can automate most of your order management and warehouse processes and provide you with better visibility of your inventory and order fulfillment rate across your warehouse locations.
- Analyze warehouse performance and efficiency: Warehouse management usually focuses on speed and accuracy. As a warehouse manager, you want your people to complete their tasks as soon as possible without any injuries or damage to any goods. But achieving speed many times comes with the high cost of “errors”. This may lead to more returns, dissatisfied customers, costly restocking, and re-delivery procedures. So, accuracy is equally important for a warehouse manager as speed.
Warehouse performance can be examined in several categories. There is performance in terms of labor and equipment handling. There are specific areas like accuracy and error reduction. And there is performance in terms of the efficient storage and handling of goods. Some of the KPIs (Key Performance Indicators) are described below:
Receiving efficiency: This determines how effective your workforce is in receiving goods and if they need the training to improve efficiency. Receiving efficiency calculates the productivity of the work being done by your employees in the receiving area of your warehouse.
Receiving cycle time: This is the time elapsed from the PO delivery received to the items being ready for sale. Receiving cycle time measures the average time taken to process received stock, which includes accounting for it, sorting it according to the category, and then storing it.
Putaway accuracy rate: Your putaway accuracy KPI tells you the percentage of the items that have been put away correctly the first time. This rate is calculated by dividing the amount of inventory that has been put away correctly by the total amount of inventory that has been put away.
Order lead time: This is simply the average length of time it takes for customers to receive orders once they are placed. The order lead time is your order cycle time plus shipping time. A shorter order lead time is better for your business.
Fulfillment accuracy rate: Order accuracy KPI is the number of orders processed accurately out of the total number of orders processed. To calculate the order accuracy rate, take the number of accurately fulfilled orders and divide it by your total number of orders. Then, multiply that number by 100 to get it to a percentage. If this rate is low, then your order management process needs to be examined and revised.
On-time Delivery: At the most basic level, you can calculate OTD as the number of units you deliver on time, divided by the total number of units you shipped: OTD = (On time units)/ (Total units). This indicator tells you how efficient your shipping processes are. It’s important to maintain a high on-time shipping rate to prevent customer dissatisfaction.
Picking accuracy: Order Picking Accuracy (OPA) is defined as the total number of orders picked and verified to be accurate before shipment divided by the total number of orders picked over the same period, as a percentage. This KPI tells you how accurately items are being picked from your warehouse for customer orders so that you can improve the overall warehouse efficiency of your order management processes.
Empty Bin Report: Empty bin report is an essential report for WMS operation. It lists all the bins which are currently empty. The empty bins report with zone, and storage section information will help the warehouse manager to assign them for the new putaway operation.
Multi-location Warehouse Best Practice
A multi-warehouse inventory management software system enables you to track inventory levels in different warehouses in real-time. Multi-warehousing allows you to store goods in different locations and still have a single point of contact who takes end-to-end responsibility for services. When an order is placed, the fulfillment center closest to that customer fulfills the order. Having multiple warehouses inherently makes it faster to fulfill the order and cheaper and faster to ship to a wider area. Implementing a system that effectively manages warehouse distribution provides more benefits and reduces risks, which will make order fulfillment more accurate, efficient, and transparent.
- Stock Replenishment Planning
You must monitor best-selling products across all the channels combined. Knowing what is selling and the rate of stock outflow, you could determine the rate of replenishment of those products. Using analytics to assess each product’s monthly selling trend, you can set up restocking systems to ensure that stocks are replenished in time and that you are never out of stock. This information will also help you evaluate which warehouse your products should be stored in, thus improving the efficiency of your overall multi-warehouse inventory management system.
- Employ the right strategies on where to keep products and route the orders
You must devise a good warehouse strategy for your multi-location warehouse to make sure you keep products in a particular warehouse not because there is a space available, but because it is the most convenient and productive to put the product in that warehouse. There are several methods you can employ for this, a few of them are outlined here:
Automatic routing of your customers’ orders to the warehouse which is close to the customers. Set up a warehouse in the region from where you get most of your orders. This will benefit you to serve your customers locally from the same region because the shipment cost and time will be less. Moreover, storing frequently purchased products in the local warehouse will help you to fulfill customers’ orders faster.
When inventory doesn’t move, there are associated carrying costs and it ties up valuable capital and resources that could otherwise be used to invest in your business. So, make sure you do not create a mess due to a huge pile of slow-moving stocks in your warehouse. Store slow-moving inventory together. Besides keeping slow-moving inventory in locations next to each other within one warehouse, you could also consider a cheaper warehouse to reduce operating costs.
Reduce the transfers between the warehouses. This will ensure that your products are moving fast. If you know some of your products are particularly popular, consider storing inventory for these items across all your warehouses. This will help you to fulfill your orders from across multiple warehouses and achieve a higher level of product movement across your warehouses.
- Keep Inventory Balanced
Keeping a balanced stock level means eliminating waste and making sure you are not keeping too much stock in the warehouse. Keeping big stock means larger capital investment which you want to avoid. You can determine stock level by analyzing data such as empty bins, order lead time, product sales, inventory turnover as well as product’s maximum, minimum, average, and reorder levels across all the warehouse locations.
- Product Stock Count in Each Warehouse Separately
It is important to count stocks at each warehouse individually. Having an overall count of your inventory will not tell which warehouse location will need replenishment. Many eCommerce sellers assume that they must only keep track of the total stock available. This will create an issue when your order will be routed to the warehouse location for fulfillment where products are not in stock.
- Inventory Management System with WMS
As your business grows, you need to make sure your software systems are integrated, and that all the data are synced all the time. This will ensure your multi-warehouse inventory management and ordering systems are in sync to prevent any delays. For a growing business, you should make sure that you have proper software solutions which can drive operations like:
- Create multiple warehouses
- Manage quantity and transfer inventory between warehouses
- Manage dropship orders
- Implement automatic order routing
- Create invoices, packing slips, and shipping labels
- Get order notifications
- Access real-time order status
You can find many interesting topics on this blog.